Die casting is popular because of its ability to regularly replicate patterns for parts that are highly complex and delicate, including those with thin-walled features. The process originated in the 19th century with casting printer parts like gears and bell cranks. Over the 20th century, the process was refined and became a cornerstone of metal component manufacturing. Xometry has offered custom die casting services for years; you can request a quote online from us at any time. Once your request comes in, our skilled team of engineers will review it and get back to you with pricing and lead times.
Since die casting uses salt cores, it can make complicated internal galleries without compromising the design or difficult tooling. Though it can be expensive and slightly limited in what it can do, Xometry customers in industries like aerospace, automotive, electronics, military, furniture—and many more!—swear by it. Read on to find out exactly why.
What is Die Casting?
The die casting process is used to turn metal from solid to molten. Like most molding methods, the melt gets injected into a mold which is made of two parts that are put together with a hydraulic press. The metal flows into the cavity between the two parts and is either heated or allowed to cool, depending on what’s being made. Sometimes the parts are water-cooled in a process called “quenching” to speed up solidification and churn out more products in less time.
Since die casting produces low-cost and high-volume light metal components, it’s common to see fully automated and intricate production lines that can consistently repeat highly precise and strong metal components. Some other processes involve higher-cost parts, sometimes of lesser quality, and can have a slower manufacturing pace.
Xometry users in the aerospace and automotive industries use the process to make engines, interiors, and housings. Although plastic has pretty much taken over as the top toy-making material, sometimes these are made from die-cast zinc alloys (although not as much as they used to be). The military uses it for vehicles, weapons, and some system components, and it’s even used in furniture-making for things like chair legs and joiners. Other parts made with die casting include electronic enclosures, heat sinks, hardware, heat distribution chassis, and decorative and structural parts. As mentioned above, it’s an important process here at Xometry—we offer a leading die casting services.
Temperatures
As previously mentioned, the molds can be either hot or cold during the casting process. Cold-chamber die casting is done with metals, such as aluminum, that have a higher melting point as well as a low volume production. In this process the metal is melted in a separate furnace, and added to the injection chamber, then a plunger moves it into the cold mold. This relies on the metal’s heat to stabilize the processing temperature. This process is cost-effective and doesn’t need as much maintenance, although there is a bigger chance of variability since it takes time for the production rate to stabilize.
Hot-chamber die casting (sometimes called goose-neck casting) is used in high-volume production. With this process, the furnace is built into the machine itself, which allows the metal to hold its temperature as it’s injected directly into the mold. Since the attached furnace eliminates the need for an injection chamber, it processes items faster. The downside is that it has a higher system cost and needs more maintenance to keep that high-quality production.
Materials
Lots of materials can be used in die casting, including alloys. Magnesium alloy die casting is one example as it can make strong and lightweight parts, as well as some of the thinnest sections possible thanks to the melt’s low viscosity. Zinc is used where strength isn’t a priority as it’s a more affordable material and easy to work with. It’s also strong enough to make parts like enclosures and toys. Copper isn’t used much in die casting because the high temperature could induce more thermal shock and it could crack. If you’re set on die-casting copper, you have to handle it very carefully and use a high-pressure process.
Pewter is a soft alloy that combines other materials. It’s mainly tin, but also has traces of copper and bismuth. It’s used for decorative objects and is easy to die cast in low-pressure equipment. In contrast, aluminum alloys are incredibly important when it comes to volume production. They do best with a hot chamber, high pressure, and more recently vacuum die casting. Aluminum provides highly precise parts that range from moderately strong to very strong.
Lead has seen a significant reduction in use, but it’s still critically important for manufacturing (ICE) automotive battery parts, particularly terminals. There’s been a lot of development in lead die casting, improving overall automation and process speeds. Similarly, tin-based alloys are seen less these days, but the need does arise from time to time. They cause very low wear and stress on tools because of the low viscosity and melting point.
Costs
The costs of starting die casting are high. It’s a complicated and expensive machine and is built to be highly durable. Since it’s so expensive, it’s not a good idea for low-volume manufacturing. That said, the happy medium for the volume to start reimbursing the higher cost of the CNC-machined parts can be as low as hundreds of parts.
Die Casting Processes
There are five common methods of die casting available.
Gravity die casting uses (obviously) gravity to feed the metal into the injection chamber. This can be done automatically, or you can even hand-ladle it. It’s good for lower complexity parts with thick sections, and the method lowers the tooling cost and equipment intricacy. Also, gravity die casting works best with aluminum for parts that are symmetrical and circular.
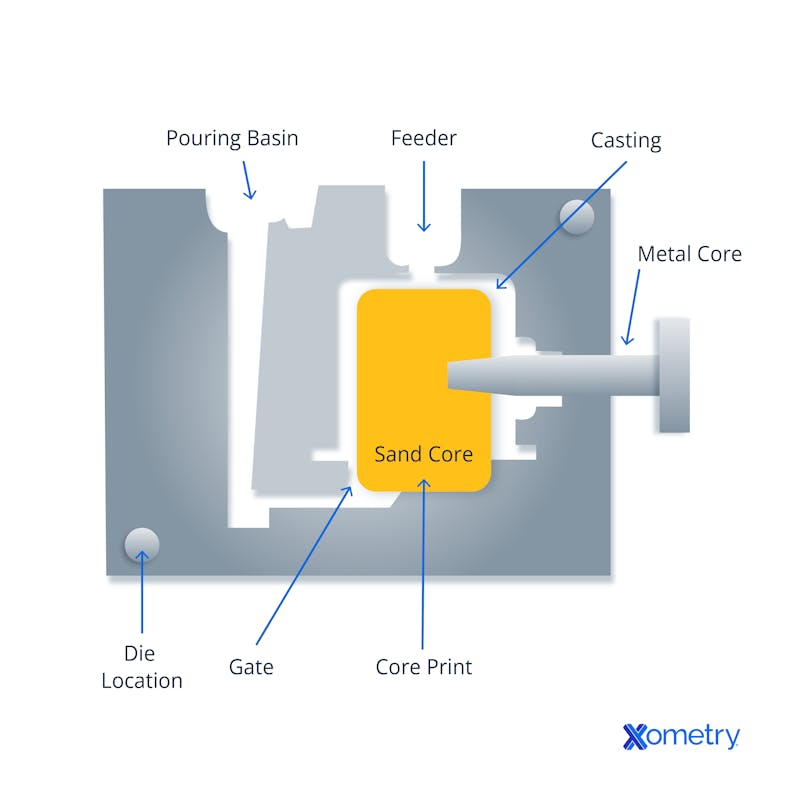
Vacuum die casting involves using a vacuum pump to remove air from the mold before adding the molten metal. The process reduces porousness and lowers turbulence, which gives a higher-quality product. Parts made with vacuum die casting are also suitable for heat treatment after casting.
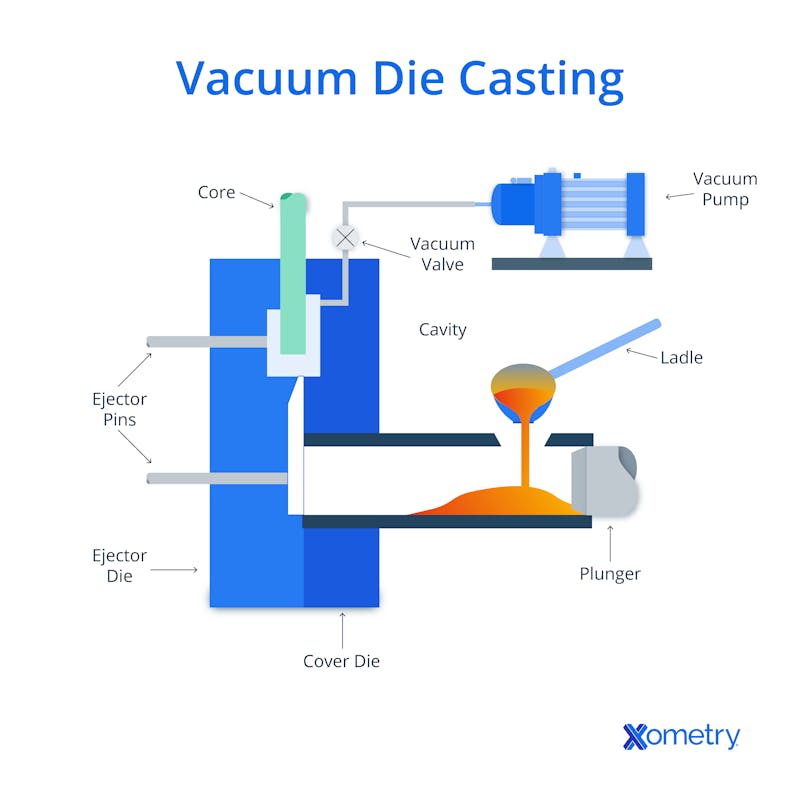
Squeeze die casting is used mostly for higher-viscosity melts. The cavity of the mold is filled before the two halves are squeezed together with high pressure until the metal solidifies. This method is helpful for ensuring the metal reaches smaller cavity areas that would be more difficult to fill with other casting methods.
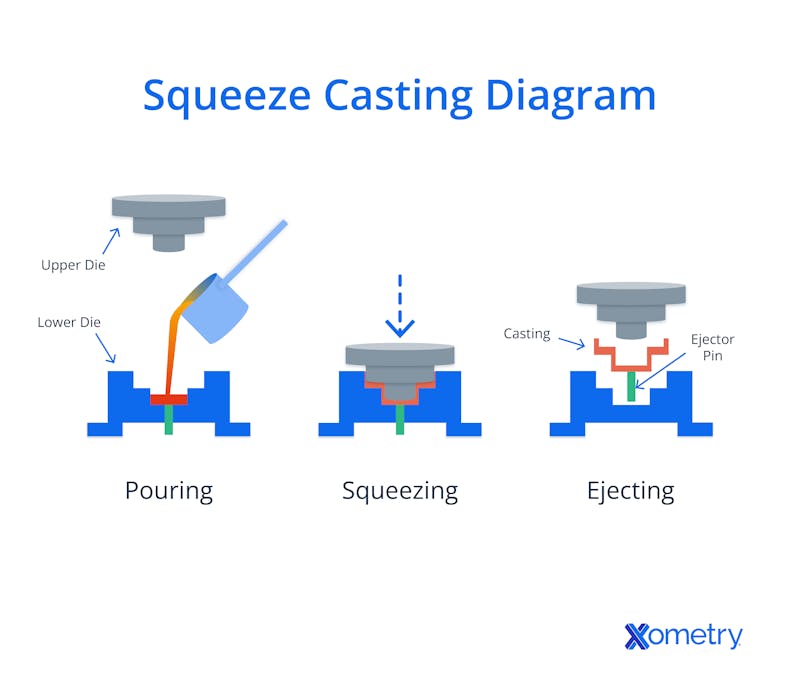
Semisolid die casting is also known as thixoforming. Unlike other casting methods, here the metal is heated until it’s in a semi-solid state, also called a thixotropic state. It gets pressure-fed into the mold cavity while still in this semi-solid state. Since it uses a lower operating temperature, processing time is shortened and accuracy is improved—most of the melt expansion happens at the time of or soon after the phase change, so there is less shrinkage.
Pressure die casting is ideal for finer and more complicated parts. It uses both high pressure and high speed to force the molten metal into the mold cavity, which makes pressure die casting more likely that the metal will reach every little space and produce a smooth finish.
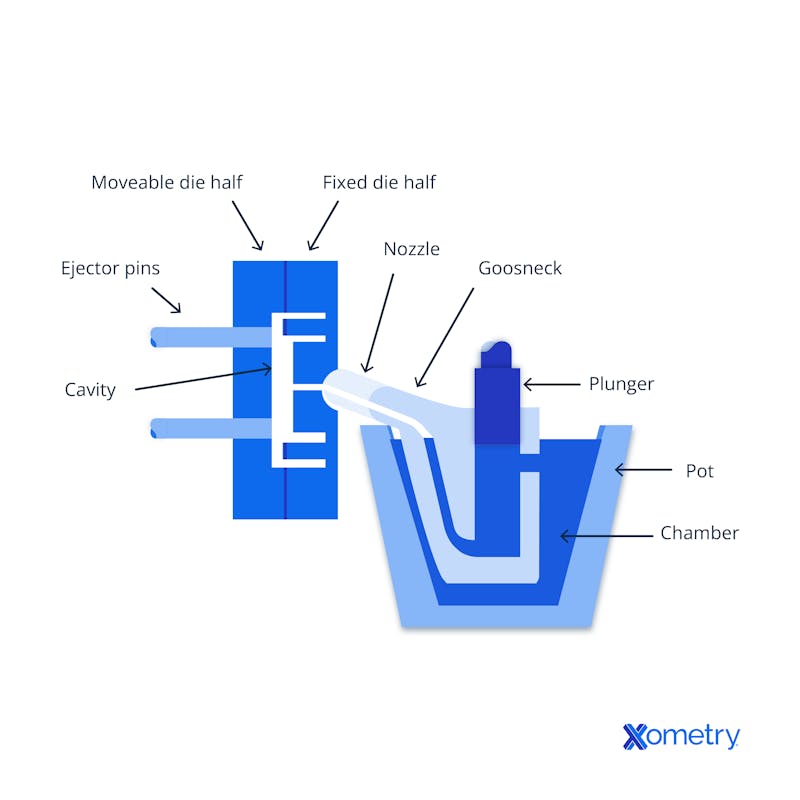
How Xometry Can Help
Among many other manufacturing offerings like CNC machining, 3D printing, laser cutting, and injection molding, Xometry also provides die casting services. If you want to learn more about this process, what materials can be used with it, or how you can use it in your business, reach out to one of our representatives today or start your quote and one of our skilled engineers will reach out to you.
Disclaimer
The content appearing on this webpage is for informational purposes only. Xometry makes no representation or warranty of any kind, be it expressed or implied, as to the accuracy, completeness, or validity of the information. Any performance parameters, geometric tolerances, specific design features, quality and types of materials, or processes should not be inferred to represent what will be delivered by third-party suppliers or manufacturers through Xometry’s network. Buyers seeking quotes for parts are responsible for defining the specific requirements for those parts. Please refer to our terms and conditions for more information.
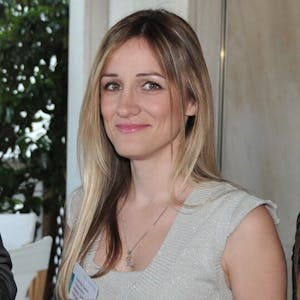