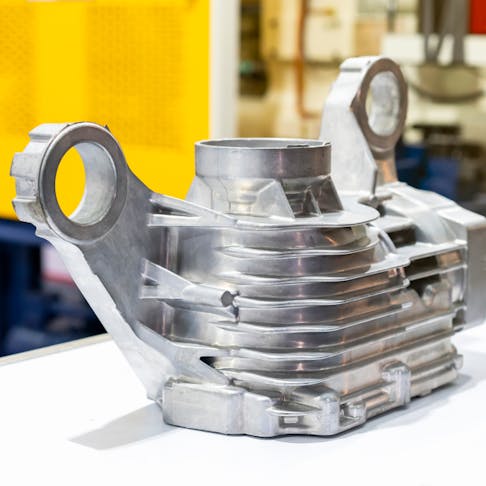
Pressure Die Casting: Types, Applications, Advantages, and Disadvantages
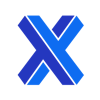
Pressure die casting is a metal casting technique that involves injecting molten metal into a mold cavity under pressure. This method is known for producing large quantities of complex, high-precision parts with excellent surface finish and dimensional accuracy, using non-ferrous metals such as aluminum, zinc, and magnesium.
This article discusses pressure die casting in detail, focusing on topics like the different pressure die casting types, their applications, advantages and disadvantages, and so much more.
What Is Pressure Die Casting?
Pressure die casting is a type of die casting method that makes use of a metal mold (usually made from premium, heat-resistant steel grades) into which a non-ferrous metal, such as aluminum, zinc, lead, magnesium, copper, or tin, is injected or introduced. This process involves forcing molten metal under pressure and high velocity into a mold cavity (die) that is machined into the desired shape. There are two forms of pressure die casting: low-pressure die casting (LPDC) and high-pressure die casting (HPDC). With LPDC, the metal is injected into the mold at low pressures, usually between 2–15 psi. HPDC injects the alloy into the mold at high pressures, usually between 1,500 and 25,400 psi. This metal manufacturing process is suitable for high-volume production of parts that are net-shaped and have tight tolerances.
How Does Pressure Die Casting Work?
Pressure die casting works as follows. Molten metal is forcefully injected under pressure into an engineered closed steel die cavity. This die is composed of two main parts: a stationary half and a moving half, both securely attached to the platens of the die casting machine. On one end, the die casting machine features an injection mechanism that employs both hydraulics and pressurized gas to propel a piston forward, thus pushing the molten metal into the steel die with precision and force. On the opposite end, the machine is equipped with a clamping mechanism that makes use of hydraulics and mechanical toggles. This mechanism is designed to withstand the significant injection pressure, ensuring the die remains firmly closed as the metal part undergoes solidification. This highly efficient process is capable of converting molten metal into a solid, near-net-shape part within mere seconds. With LPDC, the pressure that the system is placed under falls within the range of 2–15 psi, whereas for HPDC, this is between 1,500–25,400 psi. HPDC involves the rapid horizontal injection of alloy into the die through a high-speed ram, taking place within a remarkably short time frame (10–100 ms). In contrast, LPDC operates at a significantly slower pace, employing a more controlled and gentle approach in which inert gas pressure gently forces the alloy upwards into the mold. In both low-pressure and high-pressure die casting processes, the applied pressure is sustained until the metal casting has fully solidified.
To learn more, see our full guide How Casting Works.
How Are the Dies Prepared With High-Pressure Die Casting?
Initially, the die is designed and manufactured from high-grade steel to accommodate the part's specifications, including: the flow, solidification, and cooling of the molten metal. Once assembled, the die, comprising two halves — the stationary cover die and the movable ejector die — undergoes the application of a release agent to prevent molten metal adhesion and facilitate easy part removal. Preheating the die to a specific temperature before casting is crucial for minimizing thermal shock and enhancing metal flow. The die is then installed into the casting machine, in which it is aligned and clamped under force. Lubrication and cooling systems are integrated within the die to ensure smooth operation and temperature control during the casting process.
What Materials Are Used in the Process of High-Pressure Die Casting?
In the high-pressure die casting process, non-ferrous metals are predominantly used due to their excellent casting properties. The most commonly used materials in HPDC include:
- Aluminum Alloys: Aluminum is a popular pressure die casting alloy due to its inherent properties such as: being lightweight, offering dimensional stability, resisting corrosion, providing electrical conductivity, and withstanding high temperatures. Aluminum alloys are widely used in automotive, aerospace, and consumer electronics for parts like: engine components, frames, and housings. It exhibits excellent flow characteristics under high pressure when melted, yet necessitates a cold chamber system to yield high-quality castings. Commonly used aluminum alloy grades include: 380, 390, 412, 443, and 518.
- Zinc Alloys: Zinc alloys offer high strength, good ductility, and a lower melting point compared to aluminum. It is suitable for intricate shapes and thin walls in applications like: automotive components, complex gears, and decorative items. This material is compatible with both hot and cold chamber die casting systems. Widely used zinc alloys in high-pressure die casting processes are: Zamak 2, Zamak 3, and Zamak 5.
- Magnesium Alloys: Magnesium is the lightest structural metal, providing parts with the lowest weight. Magnesium also has high machinability and, due to its lower melting point, is suitable for hot chamber die casting. It is used in applications requiring high strength-to-weight ratios, such as automotive and aerospace components. Common alloys used include: AE42, AM60, AS41B, and AZ91D.
- Copper Alloys: Due to its tendency to crack, shrink, and develop porosity, pure copper is rarely used in die casting. Copper-based alloys such as: brass, bronze, and beryllium copper are more commonly employed in the die casting processes. These alloys are used for their excellent electrical conductivity, heat resistance, and corrosion resistance, suitable for electrical components, heat sinks, and other applications in which these properties are desired.
What Are the Types of Pressure Die Casting?
There are two types of pressure die casting: low-pressure die casting (LPDC) and high-pressure die casting (HPDC). Low-pressure die casting works with lower pressures, as the name suggests, and also functions with much lower speeds, whereas high-pressure die casting operates at significant speeds and pressures. Besides these classifications, pressure die casting, or die casting in general, can also be classified based on the chamber types:
- Hot Chamber: In hot chamber die casting the metal is heated inside the casting machine. It works best with lower-melting-point metals like: tin, magnesium, and lead alloys.
- Cold Chamber: Here, the metal is heated in a separate furnace and then transferred into the casting machine. This is ideal for metals with high melting points like: brass, copper, and aluminum.
To learn more, see our full guide on the Different Types of Casting.
Why Is Aluminum the Most Commonly Used Material in Pressure Die Casting?
Aluminum is the most commonly used material in pressure die casting due to its lightweight nature, excellent strength-to-weight ratio, good thermal and electrical conductivity, high corrosion resistance, and ability to withstand the highest temperatures of all the die cast alloys. Furthermore, aluminum alloys offer great dimensional stability and a wide range of surface-finishing options — more than other die cast alloys.
How Are Zinc and Magnesium Utilized in Die Casting?
Zinc and magnesium are key materials in die casting due to their specific advantages. Zinc is favored for its ability to capture intricate details and complex shapes because of its low melting point, making it perfect for small, detailed parts like gears and decorative items. It's also durable, offers great finishing options, and provides excellent corrosion resistance.
Magnesium, being the lightest die casting metal, is sought after in industries aiming to reduce weight, such as automotive and aerospace, to enhance fuel efficiency and performance. Its high strength-to-weight ratio and good mechanical properties make it ideal for producing strong, lightweight components. Magnesium, with its lower melting point, is used for hot chamber die casting, whereas zinc is compatible with both hot and cold chamber die casting.
What Are the Key Factors Affecting Mold Design in Pressure Die Casting?
The key factors affecting mold design in pressure die casting are listed below:
- The shape, size, and complexity of the part being cast influence the mold design significantly. Complex parts may require intricate mold features like: slides, cores, and collapsible cores.
- The casting material's properties, such as melting temperature, fluidity, shrinkage rate, and thermal conductivity, dictate aspects of mold design, including cooling systems and gate locations.
- The specifications of the die casting machine, such as clamping force, platen size, and injection system, must be compatible with the mold design to ensure efficient operation.
- The selection of mold material impacts the mold's life span and performance. Materials must withstand high temperatures and pressures without degrading.
- The design of the gate and runner system affects the flow of molten metal into the mold cavities, influencing the part's quality by minimizing air entrapment and ensuring complete filling.
- Proper cooling and heating channels are essential for controlling the mold temperature, which affects the casting's solidification process and cycle times.
- The ejection system must be designed with consideration for the placement and number of ejector pins, to efficiently remove the cast part from the mold without damaging the part or the mold.
- Adequate venting is necessary to allow gases to escape during the casting process, preventing defects such as porosity and blisters. Overflow systems capture excess material.
- The desired surface finish of the final part can dictate the mold's surface preparation and may influence the choice of mold material and coatings.
- The required tolerances and the part's dimensional accuracy must be considered in the mold design to ensure the cast parts meet specifications.
- Expected production volume influences mold design, particularly the mold's durability and the number of cavities, to ensure the mold can produce the required quantity of parts without significant wear.
How Does Wall Thickness Impact the Pressure Die Casting Process?
Wall thickness significantly impacts the pressure die casting process by influencing the: molten metal's flow and solidification, part quality, and production efficiency. Thinner walls allow for faster cooling and solidification, reducing cycle times and improving productivity. However, they require precise control over injection pressure and speed to ensure complete mold filling and to minimize defects. On the other hand, thicker walls slow down the cooling process, leading to longer cycle times and increased risk of defects such as porosity and shrinkage, as the interior solidifies slower than the exterior. Additionally, uneven wall thickness can cause differential cooling rates, resulting in warping or residual stresses in the final part. Balancing wall thickness is thus crucial for optimizing part strength, reducing material usage and part weight, and ensuring high-quality casting with minimal defects.
How Are Molds for High Pressure Die Cast Designed?
The design process begins with a detailed analysis of the part geometry, including considerations for: the part's function, required tolerances, and surface finish. Material properties of the alloy to be cast, such as its melting temperature, shrinkage rate, and flow characteristics, are taken into account to determine mold features like: cooling channels, gating systems, and ejection mechanisms. CAD software is typically used to create precise mold designs, allowing for simulation of the molten metal flow and solidification before the mold is manufactured. The mold design also includes allowances for thermal expansion and shrinkage of the material during casting. Key components of the mold, such as: cores, slides, and inserts, are designed to create complex geometries and undercuts in the cast part.
The gating system is carefully planned to ensure efficient metal flow into the mold cavity while venting paths are included to allow gases to escape. This prevents porosity and other defects. Moreover, cooling systems within the mold are strategically placed to regulate the temperature, facilitating rapid cooling and solidification of the cast part. The durability of the mold is considered, and high-grade steels and surface treatments that can withstand the high pressures and temperatures of the die casting process for thousands of cycles are selected. The result is a robust, precision-engineered mold that ensures high-quality, consistent casting results.
How Are Pressure Die Casting Molds Maintained?
Maintaining pressure die casting molds is crucial to ensure their longevity and consistent quality of the cast parts. Regular maintenance practices involve thorough cleaning to remove any residual metal, lubricants, and debris, preventing mold damage and ensuring clean, precise casts. Visual inspections are conducted to identify wear or damage, such as: cracks, erosion, or thermal fatigue, which could compromise mold integrity. Critical components like: ejector pins, cores, and cooling channels require special attention to ensure they operate smoothly and efficiently. Lubrication of moving parts is essential to prevent sticking and wear. Additionally, periodic checks and calibrations are necessary to ensure the mold closes correctly, maintaining proper alignment and preventing flash. Molds are also treated with protective coatings and anti-rust agents during storage to safeguard against corrosion and environmental damage.
How Is the Pressure Die Casting Process Done?
The pressure die casting process involves several key steps to transform molten metal into precise, high-quality parts:
- Clean the two halves of the die and apply a release agent to prevent the molten metal from sticking to the die surfaces. Preheat the die if necessary, depending on the metal and part complexity.
- Heat the metal alloy (commonly aluminum, zinc, magnesium, or copper-based alloys) in a furnace until it reaches its melting point.
- Transfer the molten metal to the injection system of the die casting machine. Use a piston to inject the molten metal into the die cavity at high pressure and speed. This high-pressure injection ensures the metal fills the entire cavity, even small details or thin walls. For low-pressure die casting, significantly lower speeds and pressures are used compared to high-pressure die casting.
- After the metal is injected, it begins to cool and solidify quickly due to the cold die surfaces. Maintain the pressure until the metal has solidified completely to minimize porosity and ensure dimensional accuracy.
- Once the metal has solidified, the die halves are separated, and the solidified part is ejected from the die using ejector pins.
- Remove any excess material from the part, such as: the sprue, runners, gates, and flash, through a trimming process.
- Perform any necessary secondary operations on the casting, such as: machining, painting, or assembly, depending on the part requirements.
- Conduct quality-control inspections to ensure the casting meets all specifications. Apply any necessary finishing touches, such as surface treatments or coatings, to enhance the part's appearance and performance.
What Are the Effects of Pressure Variations on the Final Product?
Pressure variations in the die casting process have a direct impact on the quality and characteristics of the final product. If the pressure is too low, the molten metal might not fully fill the mold, leading to incomplete parts or parts with poor surface detail. This can also result in increased porosity, making the castings weaker and less dense. On the other hand, excessive pressure can cause the molten metal to infiltrate the smallest crevices of the mold, leading to flash formation around the part, which requires additional processing to remove. High pressure may also contribute to accelerated wear and tear on the mold, shortening its service life. Moreover, optimal pressure is critical for achieving the desired dimensional accuracy; deviations can lead to parts that do not meet the specified tolerances, affecting their functionality and assembly with other components.
What Are the Different Applications of Pressure Die Casting?
Some of the common applications of pressure die casting are listed below:
- Automotive components (engine blocks, gearbox cases, and wheel spacers).
- Consumer electronics (smartphone frames, connectors, and housings).
- Aerospace parts (actuators, gearbox components, and engine mounts).
- Lighting fixtures (lamp housings, reflectors, and heat sinks).
- Power tools (gearboxes, motor housings, and handles).
- Sporting goods (golf clubs, bicycle frames, and fishing-reel bodies).
- Industrial machinery (pumps, valves, and compressors).
- Electrical components (connectors, switchgear, and enclosures).
- Furniture hardware (handles, knobs, and frames).
What Are the Advantages of Pressure Die Casting?
Some of the benefits and advantages of pressure die casting include:
- Ideal for high-volume manufacturing.
- This process produces parts with high precision and consistent dimensions.
- It enables the casting of complex shapes with intricate details and thin walls.
- Castings have a smooth surface directly out of the mold.
- The process can achieve tight tolerances.
- It has less waste compared to other fabrication methods that involve material removal.
- A wide range of non-ferrous metals can be used, including: aluminum, zinc, magnesium, and copper alloys.
- It can produce large quantities of parts in a short time frame.
- While the initial setup and tooling costs can be high, the per-unit cost significantly decreases for large production runs, making it cost-effective for mass production.
- HPDC allows for the casting of extremely thin-walled components — as thin as 1 mm.
What Are the Disadvantages of Pressure Die Casting?
While there are several advantages associated with pressure die casting, it also has some drawbacks, such as:
- The initial costs for tooling and setting up pressure die casting operations are high due to the complexity and precision of the molds required.
- It’s prone to porosity issues. The rapid cooling and solidification can lead to porosity in the cast parts, which might affect their mechanical strength and integrity.
- Pressure die casting is generally limited to non-ferrous metals.
- There are size limitations for cast parts due to the constraints of the die casting machines and the pressure required to fill the mold.
What Are Common Issues With Pressure Die Casting?
Five of the most common issues with pressure die casting and their solutions are discussed below:
- Porosity: Porosity in solid cast metal parts manifests as holes or voids that can vary in size from microscopic to several cubic millimeters or larger. This defect primarily stems from two causes: solidification shrinkage and gas porosity. Solidification shrinkage happens as the injected molten metal cools too swiftly, contracting against the cooler mold walls. This contraction creates voids within the cooling molten metal away from the mold walls. On the other hand, gas porosity occurs when air or gas becomes trapped within the mold, leading to the formation of pockets. This can happen under several conditions, such as inadequate venting or improper mixing of materials during the mold-filling process. To mitigate these issues, manufacturers may adjust the mold design or casting procedures to promote uniform cooling, minimize shrinkage, or lessen the chance of air entrapment. The appropriate strategy is determined based on the underlying cause of the porosity.
- Cold Shuts: Cold shuts, also known as cold laps, occur when two fronts of molten metal flow meet but do not properly fuse, resulting in a weak spot or seam. This flaw often results from inadequate gating system design or insufficient molten material fluidity. To prevent cold shuts, manufacturers can: adjust the gating system, raise the pouring temperatures, or enhance the mold's ability to vent gases.
- Misruns: Caused by insufficient molten metal flow or premature solidification before the mold is fully filled, leading to incomplete castings or parts that are not fully formed. The solution here is similar to that of cold shuts. It involves reviewing and potentially modifying the design of the mold, the configuration of the gating system, and the fluidity of the molten metal to ensure complete mold filling.
- Flash: Excess thin layers of metal that escape from the mold cavity at the parting line or around ejector pins, requiring additional trimming operations. To solve the issue of flash in die casting, it's essential to increase the clamping force of the machine to ensure mold halves are tightly sealed, regularly inspect and maintain molds for damage or misalignment, and adjust injection parameters to optimal levels. Additionally, revising mold design for better venting and thermal balance, controlling the molten metal temperature, improving the gating system, implementing consistent process controls, and using appropriate release agents can effectively minimize or eliminate flash.
- Blisters: Blisters are a type of gas porosity that manifest as visible, raised bubbles on the surface of a component. They occur when air or gas, trapped at high pressure within the casting, expands and pushes the material outward after the casting is ejected from the mold. To rectify blisters, the same approach is used for internal gas porosity: minimizing trapped air. These solutions might include: altering the mold's cooling rate, tweaking water circulation, extending the cooling period, or quenching the part immediately after it's ejected from the mold. Adjusting the temperature of the alloy to decrease the thermal disparity between the mold and the metal is another effective strategy.
Is Pressure Die Casting Cost-Effective?
Yes. High-pressure die casting is especially cost-effective for high-production runs. This method enables the production of large volumes of parts quickly, often making it the most economical choice for high-volume production. The speed and accuracy of casting cycles lead to minimal waste and high efficiency, thereby decreasing the cost per unit over time.
How Eco-Friendly Is Pressure Die Casting?
Pressure die casting, while inherently energy-intensive due to the high temperatures required to melt metals, offers several eco-friendly aspects. It is highly material-efficient, producing minimal waste due to its ability to create near-net shapes and complex parts in a single process. The metals commonly used in die casting, such as aluminum and zinc, are highly recyclable, allowing for the reuse of scrap and excess materials without degradation of their properties. This recyclability significantly reduces the environmental impact associated with raw-material extraction and processing.
Is Pressure Die Casting Environmentally Friendly?
Yes, it is considered to be one of the more environmentally friendly methods in modern manufacturing. However, even so, it’s important to take into account that pressure die casting has both environmentally friendly aspects and areas in which its environmental impact is more significant. On the positive side, it is highly efficient in material usage, producing minimal waste due to its capability to create precise, near-net-shape parts that require less machining and finishing. The process also extensively uses recyclable non-ferrous metals like aluminum and zinc, which can be melted down and reused multiple times without losing their properties, thus reducing the need for new raw-material extraction and processing.
However, pressure die casting is energy-intensive, primarily due to the high temperatures required to melt metals, which can contribute to higher carbon emissions depending on the energy source. Additionally, the production process involves the use of lubricants and release agents, some of which may have environmental implications if not properly managed.
How Does Pressure Die Casting Compare to Other Forming Processes?
Pressure die casting stands out among other forming processes for its ability to produce high volumes of complex shapes with excellent dimensional accuracy and smooth surface finishes at a rapid pace. Unlike sand casting or investment casting, pressure die casting can achieve tighter tolerances and thinner walls, making it ideal for precision components. Compared to forging or machining, it reduces material waste and can be more cost-effective for large production runs, though it generally involves higher initial tooling costs.
Is High Pressure Die Casting Efficient?
Yes. High-pressure die casting is considered to be both efficient and economical.
What Are the Long-Term Implications in the Manufacturing Sector?
The long-term implications of pressure die casting in the manufacturing sector involve: increased automation, efficiency, and a push towards sustainability. As technology advances, this process continues to offer a pathway to producing high-quality, complex parts at scale, with significant material and efficiency benefits.
Is High Pressure Die Casting Safe To Use?
It depends. High-pressure die casting is generally safe when proper safety protocols and equipment are in place. The process involves handling molten metals and operating heavy machinery, which inherently carry risks such as: burns, exposure to harmful gases, and equipment-related injuries. However, adherence to rigorous safety standards, including the use of personal protective equipment (PPE), regular maintenance of machinery, and thorough training for operators, significantly mitigate these risks. With these precautions, high-pressure die casting can be performed safely.
What Are the Safety Considerations in Pressure Die Casting?
The safety considerations in pressure die casting are very important due to the inherent risks associated with handling molten metal and operating high-pressure machinery. Key safety measures include wearing appropriate PPE such as: heat-resistant gloves, face shields, and safety glasses to protect against burns, splashes, and flying debris. Proper ventilation is crucial to prevent exposure to harmful gases and fumes released during casting. Regular equipment maintenance and safety inspections are also essential to ensure machinery operates correctly and safely. Operators must be thoroughly trained in machine operation, emergency procedures, and hazard recognition to mitigate risks of accidents.
What Is the Difference Between Pressure Die Casting and Gravity Die Casting?
The key difference between pressure die casting and gravity die casting lies in how the molten metal is introduced into the mold. When you use gravity die casting, molten metal is poured into the mold from above and fills it under the force of gravity alone. In contrast, pressure die casting, including both LPDC and HPDC variants, involves forcing molten metal into the mold under pressure, ranging from 2 psi in LPDC to between 1,500 and 25,400 psi in HPDC, with the pressure maintained until the metal solidifies.
What Is the Difference Between Pressure Die Casting and Squeezing Die Casting?
The main difference between pressure die casting and squeeze casting lies in the method of introducing and solidifying the molten metal within the mold. Pressure die casting involves injecting molten metal into a mold under pressure, rapidly filling the mold cavities, and then maintaining pressure until the metal solidifies. In contrast, when you use squeeze casting, also known as liquid metal forging, involves pouring molten metal into an open mold and then applying high pressure to the molten pool via a hydraulic press as it solidifies. This pressure is maintained during the entire solidification process, leading to denser, higher-quality castings with fewer porosities compared to traditional high-pressure die casting.
Summary
This article presented pressure die casting, explained it, and discussed its various types and applications. To learn more about pressure die casting, contact a Xometry representative.
Xometry provides a wide range of manufacturing capabilities, including casting and other value-added services for all of your prototyping and production needs. Visit our website to learn more or to request a free, no-obligation quote.
Disclaimer
The content appearing on this webpage is for informational purposes only. Xometry makes no representation or warranty of any kind, be it expressed or implied, as to the accuracy, completeness, or validity of the information. Any performance parameters, geometric tolerances, specific design features, quality and types of materials, or processes should not be inferred to represent what will be delivered by third-party suppliers or manufacturers through Xometry’s network. Buyers seeking quotes for parts are responsible for defining the specific requirements for those parts. Please refer to our terms and conditions for more information.
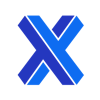