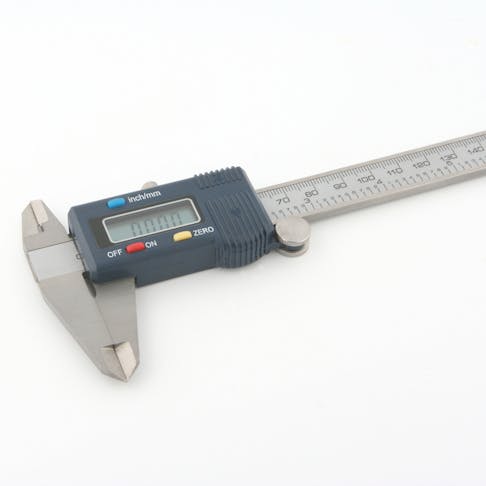
ISO 2768 Certification: Definitions, Industries, Processes
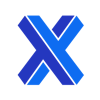
One internationally recognized standard that addresses tolerances in technical drawings is ISO 2768. ISO 2768 provides guidelines for general tolerances, ensuring compatibility and functionality across various industries and applications. This article will discuss ISO 2768 certification, exploring its definition, its relevance in different industries, and an overview of the process.
What Is ISO 2768?
ISO 2768 is an international standard developed by the International Organization for Standardization (ISO). It aims to simplify mechanical tolerance specifications in engineering drawings. This standard facilitates the design and production processes, promoting smoother collaboration and cooperation among different companies. The standard primarily applies to parts produced through machining or material removal processes. When tolerance ranges are not explicitly specified for a particular dimension, ISO 2768 should be followed.
The ISO 2768 standards are relevant to a wide range of industries. ISO 2768 is relevant to a wide range of manufacturing industries and products, including the: automotive, aerospace, electronics, and electrical industries.
What Types of Tolerances Does ISO 2768 Cover?
ISO 2768 is divided into two sections: ISO 2768-1 and ISO 2768-2. These sections establish standards for mechanical precision, with the goal of simplifying technical drawings. ISO 2768-1 is entitled "General tolerances for linear and angular dimensions," which defines precision levels categorized as fine (f), medium (m), coarse (c), and very coarse (v). ISO 2768-2 focuses on "Geometrical tolerances for features," and uses different precision levels or tolerance classes: H, K, and L.
As an example, if a drawing specifies ISO 2768-mK, it means that the component must adhere to a “medium” tolerance range for ISO 2768-1 and the "K" tolerance class for ISO 2768-2. ISO 2768-mK is commonly utilized in the manufacturing of sheet metal components, while manufacturers of machined components may opt for ISO 2768-fH. Both ISO 2768 part 1 and part 2 are discussed in further detail in the sections below:
Linear Dimensions
Table 1 defines tolerance standards for linear dimensions. Since the nominal feature lengths only start at 0.5 mm, designers are required to indicate any nominal sizes smaller than 0.5 mm next to the corresponding size.
Nominal feature length (mm) | Tolerance Class Designation (Description) Permissible dimensional deviation in mm | Tolerance Class Designation (Description) Permissible dimensional deviation in mm | Tolerance Class Designation (Description) Permissible dimensional deviation in mm | Tolerance Class Designation (Description) Permissible dimensional deviation in mm |
---|---|---|---|---|
Tolerance Class Designation (Description)
Permissible dimensional deviation in mm Fine (f) | Tolerance Class Designation (Description)
Permissible dimensional deviation in mm Medium (m) | Tolerance Class Designation (Description)
Permissible dimensional deviation in mm Coarse (c) | Tolerance Class Designation (Description)
Permissible dimensional deviation in mm Very coarse (v) | |
Nominal feature length (mm) 0.5 up to 3 | Tolerance Class Designation (Description)
Permissible dimensional deviation in mm ±0.05 | Tolerance Class Designation (Description)
Permissible dimensional deviation in mm ±0.1 | Tolerance Class Designation (Description)
Permissible dimensional deviation in mm ±0.2 | Tolerance Class Designation (Description)
Permissible dimensional deviation in mm - |
Nominal feature length (mm) Over 3 up to 6 | Tolerance Class Designation (Description)
Permissible dimensional deviation in mm ±0.05 | Tolerance Class Designation (Description)
Permissible dimensional deviation in mm ±0.1 | Tolerance Class Designation (Description)
Permissible dimensional deviation in mm ±0.3 | Tolerance Class Designation (Description)
Permissible dimensional deviation in mm ±0.5 |
Nominal feature length (mm) Over 6 up to 30 | Tolerance Class Designation (Description)
Permissible dimensional deviation in mm ±0.1 | Tolerance Class Designation (Description)
Permissible dimensional deviation in mm ±0.2 | Tolerance Class Designation (Description)
Permissible dimensional deviation in mm ±0.5 | Tolerance Class Designation (Description)
Permissible dimensional deviation in mm ±1.0 |
Nominal feature length (mm) Over 30 up to 120 | Tolerance Class Designation (Description)
Permissible dimensional deviation in mm ±0.15 | Tolerance Class Designation (Description)
Permissible dimensional deviation in mm ±0.3 | Tolerance Class Designation (Description)
Permissible dimensional deviation in mm ±0.8 | Tolerance Class Designation (Description)
Permissible dimensional deviation in mm ±1.5 |
Nominal feature length (mm) Over 120 up to 400 | Tolerance Class Designation (Description)
Permissible dimensional deviation in mm ±0.2 | Tolerance Class Designation (Description)
Permissible dimensional deviation in mm ±0.5 | Tolerance Class Designation (Description)
Permissible dimensional deviation in mm ±1.2 | Tolerance Class Designation (Description)
Permissible dimensional deviation in mm ±2.5 |
Nominal feature length (mm) Over 400 up to 1000 | Tolerance Class Designation (Description)
Permissible dimensional deviation in mm ±0.3 | Tolerance Class Designation (Description)
Permissible dimensional deviation in mm ±0.8 | Tolerance Class Designation (Description)
Permissible dimensional deviation in mm ±2.0 | Tolerance Class Designation (Description)
Permissible dimensional deviation in mm ±4.0 |
Nominal feature length (mm) Over 1000 up to 2000 | Tolerance Class Designation (Description)
Permissible dimensional deviation in mm ±0.5 | Tolerance Class Designation (Description)
Permissible dimensional deviation in mm ±1.2 | Tolerance Class Designation (Description)
Permissible dimensional deviation in mm ±3.0 | Tolerance Class Designation (Description)
Permissible dimensional deviation in mm ±6.0 |
Nominal feature length (mm) Over 2000 up to 4000 | Tolerance Class Designation (Description)
Permissible dimensional deviation in mm – | Tolerance Class Designation (Description)
Permissible dimensional deviation in mm ±2.0 | Tolerance Class Designation (Description)
Permissible dimensional deviation in mm ±4.0 | Tolerance Class Designation (Description)
Permissible dimensional deviation in mm ±8.0 |
Table Credit: https://dekmake.b-cdn.net/
Nominal feature length (mm) | Tolerance Class Designation (Description) Permissible dimensional deviation in mm | Tolerance Class Designation (Description) Permissible dimensional deviation in mm | Tolerance Class Designation (Description) Permissible dimensional deviation in mm | Tolerance Class Designation (Description) Permissible dimensional deviation in mm |
---|---|---|---|---|
Tolerance Class Designation (Description)
Permissible dimensional deviation in mm Fine (f) | Tolerance Class Designation (Description)
Permissible dimensional deviation in mm Medium (m) | Tolerance Class Designation (Description)
Permissible dimensional deviation in mm Coarse (c) | Tolerance Class Designation (Description)
Permissible dimensional deviation in mm Very coarse (v) | |
Nominal feature length (mm) 0.5 up to 3 | Tolerance Class Designation (Description)
Permissible dimensional deviation in mm ±0.5 | Tolerance Class Designation (Description)
Permissible dimensional deviation in mm ±0.2 | Tolerance Class Designation (Description)
Permissible dimensional deviation in mm ±0.4 | Tolerance Class Designation (Description)
Permissible dimensional deviation in mm ±0.4 |
Nominal feature length (mm) Over 3 up to 6 | Tolerance Class Designation (Description)
Permissible dimensional deviation in mm ±0.5 | Tolerance Class Designation (Description)
Permissible dimensional deviation in mm ±0.5 | Tolerance Class Designation (Description)
Permissible dimensional deviation in mm ±1.0 | Tolerance Class Designation (Description)
Permissible dimensional deviation in mm ±1.0 |
Nominal feature length (mm) Over 6 | Tolerance Class Designation (Description)
Permissible dimensional deviation in mm ±1.0 | Tolerance Class Designation (Description)
Permissible dimensional deviation in mm ±1.0 | Tolerance Class Designation (Description)
Permissible dimensional deviation in mm ±2.0 | Tolerance Class Designation (Description)
Permissible dimensional deviation in mm ±2.0 |
Table Credit: https://dekmake.b-cdn.net/
Ranges of nominal lengths in mm | Flatness/ Straightness Tolerance Class H | Flatness/ Straightness Tolerance Class K | Flatness/ Straightness Tolerance Class L |
---|---|---|---|
Ranges of nominal lengths in mm Up to 10 | Flatness/ Straightness Tolerance Class H 0.02 | Flatness/ Straightness Tolerance Class K 0.05 | Flatness/ Straightness Tolerance Class L 0.1 |
Ranges of nominal lengths in mm Above 10 to 30 | Flatness/ Straightness Tolerance Class H 0.05 | Flatness/ Straightness Tolerance Class K 0.1 | Flatness/ Straightness Tolerance Class L 0 |
Ranges of nominal lengths in mm Above 30 to 100 | Flatness/ Straightness Tolerance Class H 0.10 | Flatness/ Straightness Tolerance Class K 0.2 | Flatness/ Straightness Tolerance Class L 0.4 |
Ranges of nominal lengths in mm Above 100 to 300 | Flatness/ Straightness Tolerance Class H 0.2 | Flatness/ Straightness Tolerance Class K 0.4 | Flatness/ Straightness Tolerance Class L 0.8 |
Ranges of nominal lengths in mm Above 300 to 1000 | Flatness/ Straightness Tolerance Class H 0.3 | Flatness/ Straightness Tolerance Class K 0.6 | Flatness/ Straightness Tolerance Class L 1.2 |
Ranges of nominal lengths in mm Above 1000 to 3000 | Flatness/ Straightness Tolerance Class H 0.4 | Flatness/ Straightness Tolerance Class K 0.8 | Flatness/ Straightness Tolerance Class L 1.6 |
Table Credit: https://dekmake.b-cdn.net/
For instance, when designing a compressor base, it is crucial to consider contact surfaces between the base and the engine, as well as between the compressor and the base. These considerations will assist in specifying the appropriate ranges of flatness in the drawings.
Straightness tolerances, on the other hand, govern the deviation of a surface from a specified line. It also regulates the allowable amount of twist and bend.
Perpendicularity
Perpendicularity is a dimensional characteristic measured in units of distance such as millimeters. The general tolerance standards for perpendicularity are summarized in Table 4:
Ranges of nominal lengths in mm | Tolerance Class H | Tolerance Class K | Tolerance Class L |
---|---|---|---|
Ranges of nominal lengths in mm Up to 100 | Tolerance Class H 0.2 | Tolerance Class K 0.4 | Tolerance Class L 1 |
Ranges of nominal lengths in mm Above 100 to 300 | Tolerance Class H 0.30 | Tolerance Class K 0.6 | Tolerance Class L 1 |
Ranges of nominal lengths in mm Above 300 to 1000 | Tolerance Class H 0.4 | Tolerance Class K 0.8 | Tolerance Class L 1.5 |
Ranges of nominal lengths in mm Above 1000 to 3000 | Tolerance Class H 0.5 | Tolerance Class K 1 | Tolerance Class L 2 |
Table Credit: https://dekmake.b-cdn.net/
Ranges of nominal lengths in mm | Tolerance Class H | Tolerance Class K | Tolerance Class L |
---|---|---|---|
Ranges of nominal lengths in mm Up to 100 | Tolerance Class H 0.50 | Tolerance Class K 0.6 | Tolerance Class L 0.6 |
Ranges of nominal lengths in mm Above 100 to 300 | Tolerance Class H 0.5 | Tolerance Class K 0.6 | Tolerance Class L 1 |
Ranges of nominal lengths in mm Above 300 to 1000 | Tolerance Class H 0.5 | Tolerance Class K 0.8 | Tolerance Class L 1.5 |
Ranges of nominal lengths in mm Above 1000 to 3000 | Tolerance Class H 0.5 | Tolerance Class K 1 | Tolerance Class L 2 |
Table Credit: https://dekmake.b-cdn.net/wp-content/uploads/ISO-2768.pdf
Ranges of nominal lengths in mm | Tolerance Class H | Tolerance Class K | Tolerance Class L |
---|---|---|---|
Ranges of nominal lengths in mm Up to 100 | Tolerance Class H 0.1 | Tolerance Class K 0.2 | Tolerance Class L 0.5 |
Table Credit: https://dekmake.b-cdn.net/
What Industries and Companies Is ISO 2768 Relevant for?
ISO 2768 is relevant for a wide range of industries and companies that deal with technical drawings and manufacturing processes. These include:
- Mechanical Engineering Services: Highly applicable in mechanical engineering services where precise tolerances are crucial for the proper functioning of mechanical components, machinery, and equipment.
- Manufacturing: Relevant to most manufacturing industries, including automotive, aerospace, consumer goods, electronics, and more. It helps ensure consistency and compatibility of parts and components produced by different manufacturers or suppliers.
- Industrial Design: Relevant for companies involved in industrial design, as it provides guidelines for specifying tolerances in technical drawings to ensure proper fit and functionality of designed products.
- Tooling and Mold-Making: Companies involved in the tooling and mold-making industries use ISO 2768 to establish tolerances for molds, dies, and tooling components, ensuring accurate replication of shapes and dimensions.
- Architecture and Construction: ISO 2768 can also be applied in the architecture and construction industries for ensuring tolerances in building components and structural elements.
What Are the ISO 2768 Audit Criteria?
ISO 2768 does not have a formal audit process or audit criteria. ISO 2768 is a standard that provides general tolerances for linear and angular dimensions in technical drawings. There is no associated certification or audit process.
ISO 2768 is typically used as a reference in technical drawings to specify acceptable tolerances for dimensions. Compliance with ISO 2768 is usually assessed through self-declaration by the organization or individual responsible for the design and manufacturing processes.
The ISO 2768 Audit and Accreditation Process
ISO 2768 does not have an audit or accreditation process because it is not a certification standard. However, other ISO standards, such as ISO 9001 for quality management systems, may include a requirement to use ISO 2768 tolerancing standards. Each ISO standard has its own audit and certification process. There are three types of audits that are relevant to maintaining ISO certification and assessing the effectiveness of company operations and processes:
- First-Party Audit (Internal Audit): This audit is conducted within your organization by internal auditors or a designated department/section. It evaluates compliance with ISO standards such as ISO 9001, ISO 14001, or ISO 45001. It can also serve as a “gap analysis” process to identify areas for improvement. Common areas checked during an internal audit include quality policy, objectives, risk management, document control, resources, and operational processes.
- Second-Party Audit (Supplier Audit): This audit is performed by the purchaser or customer on a supplier or company providing products or services. It is typically conducted to assess critical products or services and evaluate the impact of supplier processes on the purchaser's operations. Supplier audits should be planned and communicated to the supplier, and they can be based on ISO standards or other relevant criteria specified by the purchaser.
- Third-Party Audit (Certification Audit): This audit is carried out by auditors from a certification body. Its purpose is to assist your organization in achieving ISO certification. The certification body must be accredited by a recognized accreditation body. Certification audits are typically conducted in two stages. The first stage verifies the completeness of documents. The second stage examines objective evidence to ensure compliance with the ISO standard. If there are no major findings, the certification body recommends certification and an ISO certificate is issued for a period of three years. Subsequent surveillance audits are conducted to ensure ongoing execution and a re-certification audit occurs after the third year.
The specific requirements and processes may vary slightly depending on the ISO standard and the certification body involved.
What Are the Benefits of a ISO 2768 Certification?
ISO 2768 is a general tolerance standard for linear and angular dimensions in technical drawings. Using ISO 2768 as a reference in technical drawings can offer several advantages for organizations. Here are some benefits of applying ISO 2768 standards in technical drawings:
- Interchangeability: ISO 2768 provides standardized tolerance values, ensuring that parts produced by different manufacturers or suppliers can fit together properly. This promotes the interchangeability and compatibility of components, making assembly and maintenance easier.
- Cost Reduction: By following the tolerance guidelines outlined in ISO 2768, organizations can minimize the need for costly customizations or adjustments. Standardized tolerances reduce the risk of errors, rework, and rejected parts, leading to cost savings in production.
- Design Consistency: ISO 2768 promotes consistency in the design process by providing a set of predefined tolerances. This helps designers and engineers maintain uniformity in their drawings, ensuring that specifications are clear and consistent across different projects. It also helps designers to avoid errors.
- Quality Control: ISO 2768 helps organizations maintain quality control by specifying acceptable tolerances for dimensions. By adhering to these standards, organizations can ensure that their products meet the required quality standards and customer expectations.
- International Compatibility: ISO standards, including ISO 2768, are globally recognized and accepted. Using ISO 2768 in technical drawings enhances international compatibility, as it provides a common reference for dimensions and tolerances across different countries and industries.
When Are ISO 2768 Certifications Required?
ISO 2768 serves as a reference for specifying tolerances in technical drawings, helping organizations ensure the interchangeability and accuracy of dimensions. It provides a set of default tolerances that can be applied to non-critical dimensions, allowing organizations to communicate their dimensional requirements effectively.
While no certification is available for implementing and using ISO 2768, organizations may need to comply with specific industry standards or regulations that reference ISO 2768 or similar tolerance standards. These industry-specific standards could include higher-level quality system approaches and standards that mandate adherence to certain tolerances and may require certification or compliance assessments.
What Accrediting Body Issues ISO 2768 Certifications?
ISO 2768 is not a certification standard but rather a general tolerance standard for linear and angular dimensions in technical drawings. It provides a set of tolerances that can be applied to various dimensions to ensure the interchangeability of parts and the accuracy of measurements.
ISO 2768 is issued and maintained by the International Organization for Standardization (ISO), which is a non-governmental organization composed of national standards bodies from different countries. ISO develops and publishes a wide range of standards covering many industries and areas of focus.
Similar Certifications and Accreditations to ISO 2768
While ISO 2768 standard pertains to general tolerances in technical drawings, there are other certifications and accreditations related to quality management systems and product standards that may be relevant in different industries. Here are a few examples:
- ISO 9001: This is the most widely recognized standard for quality management systems. It sets criteria that organizations can use to demonstrate their ability to consistently provide products and services that meet customer requirements and regulatory standards. ISO 9001 focuses on overall quality management principles and processes.
- ISO 14001: This standard addresses environmental management systems. It provides guidelines that organizations can follow to establish, implement, maintain, and improve their environmental management systems, helping them manage their environmental responsibilities and minimize their environmental impact.
- ISO/IEC 17025: This accreditation is specific to testing and calibration laboratories. ISO/IEC 17025 sets criteria for judging the competence, impartiality, and consistent operation of laboratories, ensuring that they can produce accurate and reliable test results. It covers factors such as equipment calibration, quality control, and personnel competence.
- AS9100: This standard is specific to the aerospace industry. AS9100 incorporates the requirements of ISO 9001 and adds additional criteria specific to aerospace organizations. It focuses on quality management systems within the aerospace industry, including risk management, configuration control, and supply chain management.
- ISO/TS 16949: This technical specification is designed for the automotive industry. It outlines the quality management system requirements for organizations involved in the design, development, production, installation, and servicing of automotive-related products. ISO/TS 16949 places a strong emphasis on process control and continuous improvement.
- ISO 13485: This standard is specific to medical devices. ISO 13485 outlines requirements for quality management systems in the design, development, production, and distribution of medical devices. It focuses on meeting regulatory and customer requirements related to the safety and effectiveness of medical devices.
Summary
This article presented the ISO 2768 certification, explained it, and discussed the various industries its relevant. To learn more about the ISO 2768 certification, contact a Xometry representative.
Xometry provides a wide range of manufacturing capabilities and other value-added services for all of your prototyping and production needs. Visit our website to learn more or to request a free, no-obligation quote.
Disclaimer
The content appearing on this webpage is for informational purposes only. Xometry makes no representation or warranty of any kind, be it expressed or implied, as to the accuracy, completeness, or validity of the information. Any performance parameters, geometric tolerances, specific design features, quality and types of materials, or processes should not be inferred to represent what will be delivered by third-party suppliers or manufacturers through Xometry’s network. Buyers seeking quotes for parts are responsible for defining the specific requirements for those parts. Please refer to our terms and conditions for more information.
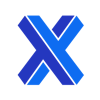