Our Ultimate Guide to Manufacturing Across Your Product Development Cycle
While many companies claim to provide manufacturing on demand, very few come close to Xometry when it comes to truly delivering against scalable capacity of production-as-a-service, fast turns on quoting and production, and uncompromising high-quality products.
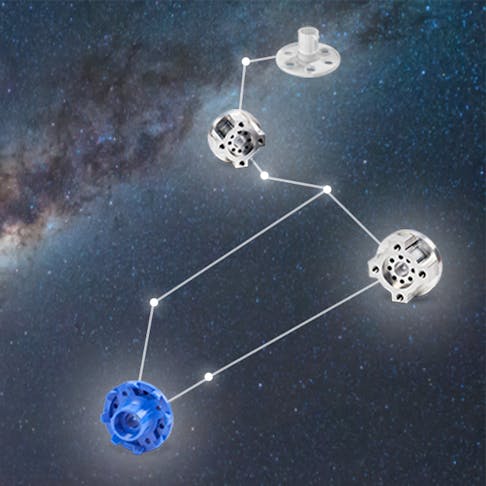
Xometry’s mission is to serve all engineers and creators across all industries with the most comprehensive, on-demand digital manufacturing platform. This means providing services for each stage of the product development process, from prototyping all the way through to production.
Xometry's vast Supplier Network provides a full range of industrial manufacturing capabilities while our machine learning-trained Xometry Instant Quoting Engine℠ puts big data to work to give you pricing and lead times in just seconds.
For engineers whose designs undergo a rigorous multi-stage engineering validation process, we have created a general guide to choosing the best manufacturing services to utilize at each product development stage. Note that this is only a general guide and the best process and material for a given project are highly dependent on the goals and specifications of a project.
Process | Cost | Lead Time | Use Case |
---|---|---|---|
Process Fused deposition modeling (FDM) | Cost $ | Lead Time 1 day | Use Case Basic form and fit verification |
Process HP Multi Jet Fusion (MJF) | Cost $ | Lead Time 1 day | Use Case Higher resolution form and fit |
Process Selective laser sintering (SLS) | Cost $ | Lead Time 1 day | Use Case Higher resolution form and fit |
Process Metal Binder Jetting | Cost $$ | Lead Time 10 days | Use Case Metal prototypes with complex geometry |
Process Rapid CNC machining | Cost $$$ | Lead Time 4 days | Use Case A prototype in the end material for preliminary durability tests |
Process Rapid sheet metal fabrication | Cost $$ | Lead Time 4 days | Use Case A prototype in the end material for preliminary durability tests |
Process Urethane Casting | Cost $$$ | Lead Time 15 days | Use Case High fidelity prototyping |
These 3D printing processes can build parts that cost as little as $5 per part but be careful to choose general-purpose materials versus specialty materials, which can dramatically increase costs early on. When 3D printing is not an option and proof of concept prototypes must be created in the end material to validate physical properties like weight, surface finish, and some basic functions, manufacturing processes like CNC machining, sheet metal fabrication, and injection molding can be set-up and shipped quickly. However, typically even the simplest machine and tool set-ups will cost more than 3D printing.
Engineering Validation Test (EVT)
At this stage of product development, you'll likely have iterated on your design and come to a final geometry that meets the specifications set forth in the product requirement document. In this stage, you’ll want to choose the materials and manufacturing processes that can be verified against all the functions and metrics set for your product. Custom manufactured components will be tested alongside PCB circuitry for thermal, power, and EMI stresses.
The manufacturing capabilities best suited for this are:
Process | Cost | Lead Time | Use Case |
---|---|---|---|
Process Stereolithography | Cost $ | Lead Time 3 days | Use Case Fit-check parts that need beautiful surface finish, high resolution, and clear finishes |
Process PolyJet | Cost $$ | Lead Time 2 days | Use Case Fit-check parts that need beautiful surface finish, high resolution, and multi-material composition |
Process Carbon DLS | Cost $$$ | Lead Time 6 days | Use Case End-use parts that need specialized properties like high heat deflection, high flexibility, or biocompatibility |
Process Direct Metal Laser Sintering | Cost $$$ | Lead Time 6 days | Use Case End-use parts that need complex metal geometries that would be cost-prohibitive with CNC machining |
Process CNC machining | Cost $$$ | Lead Time 4 days | Use Case End-use parts that need the high impact and fatigue resistance of metals, coupled with a variety of unique properties depending on the alloy |
Process Sheet metal fabrication | Cost $$ | Lead Time 3 days | Use Case End-use parts that need durable enclosures, brackets, and panels with a variety of corrosion resistance, flex, and durability properties. |
Process Rapid injection molding | Cost $$$$ | Lead Time 15 days | Use Case A high fidelity prototype in the end material for preliminary durability tests |
Process Urethane casting | Cost $$$ | Lead Time 15 days | Use Case A prototype with similar properties as the end material for preliminary durability tests |
Design Validation Test (DVT)
This is the penultimate testing stage in a comprehensive product development process during which engineers test parts for maximal stresses including impact resistance, fire resistance, chemical resistance, waterproofing, and more. This phase may still lead to additional iterations to the hardware, and, importantly, ensure all materials and manufacturing processes meet the certification requirements such as UL, FCC, CE, and more.
The manufacturing certifications Xometry can offer include:
- ITAR/EAR Registration
- ASD 9100 Certification
- ISO 9001:2015 Certification
- ISO 13485 Certification
- NADCAP
- Certificate of Conformance
- Material and Process Lot Traceability
- Hardware Certifications
These certifications are the standard choices in the Xometry Instant Quoting Engine℠. If other certifications are required to be in compliance with US product standards, such as the 3A Sanitary Standards, then Xometry manufacturing experts can provide advice on how to best optimize the materials, design, and inspections to meet these standards.
Production Validation Testing (PVT)
During production validation testing, the product is soft-launched with a batch of up to 500 units. This is the stage during which it becomes critical to ensure the production of the units are reliable so that there are no manufacturing defects or inefficiencies that drive up costs. Consulting with the manufacturing experts at Xometry can help optimize production and assembly processes.
Manufacturing Design
The manufacturing design stage is critical to ensuring your investment pays off. Xometry manufacturing experts can help you define your specifications, suggest inspections, and ensure everything is ready before investing in production. Consult our teams dedicated to the following areas of expertise:
- Injection molding design and tooling
- 3D printing and urethane casting
- CNC machining optimization
- Sheet metal fabrication optimization
You can reach out to our support team with your quote ID number or submit a quote for manual review for any of these teams to automatically reach out.
Assembly Design
Less well known at Xometry are our assembly services. For any project in any process, we are able to source a manufacturing supplier from coast to coast, or even from around the world, to assemble product units. Whether you need to add in simple metal threaded inserts or combine components incorporating parts from different technologies including 3D printing, CNC machining, and sheet metal fabrication, Xometry has the ability to streamline the tail end of the production process and deliver finished products.
Want more details? Browse our design guides for additional expert, process-specific design and manufacturing tips.
Want to know our tolerances? See our manufacturing standards for details by process.
Dig deeper into materials. See our full catalog of industrial-grade manufacturing materials for additional details and spec sheets.
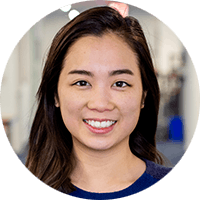