Sheet metal fabrication is an ideal process for creating durable parts, from single prototypes to high-volume production runs.
Sheet metal has many commercial applications and can be a cost-effective way to create your parts. However, because sheet metal parts are made from a single, flat sheet, there are additional design considerations compared to other machining processes.
To help you save time and money, here are 5 tips you can use on your next project!
1. Choose the Appropriate Material
Material cost is one of the most significant drivers of part costs. Be sure to choose your material carefully and use stock sizes. If you are prototyping, consider using Aluminum 5052 versus 304 stainless steel or other less expensive material.
Check out our list of available materials.
2. Design to a Common Gauge
When designing your part, remember to use standard sheet metal gauges. Generally, Xometry is capable of manufacturing sheet metal parts up to ¼” (6.35mm) in thickness, but this constraint mainly depends on the geometry of the part. Thicker metals may restrict what bends are achievable for your part.
3. Simplify Your Folds
In general, the more complicated your part is, the more expensive it will be. To cut down on your costs, design for simple angled bends, with a radius equal to or greater than the thickness of the sheet. Small bends on large, thick parts tend to become inaccurate, so they should be avoided if possible. Our Design Guide on sheet metal gives some great best practices for designing sheet metal pieces.
4. Limit the Use of Tight Tolerances
Typically, only a few surfaces of a part are critical to its function. The more features with tolerance callouts in the design (e.g., radii, hole diameters, and distances), the more expensive a part becomes to manufacture. In order to eliminate unnecessary costs, the key is to only assign tolerances to mission critical features and surfaces.
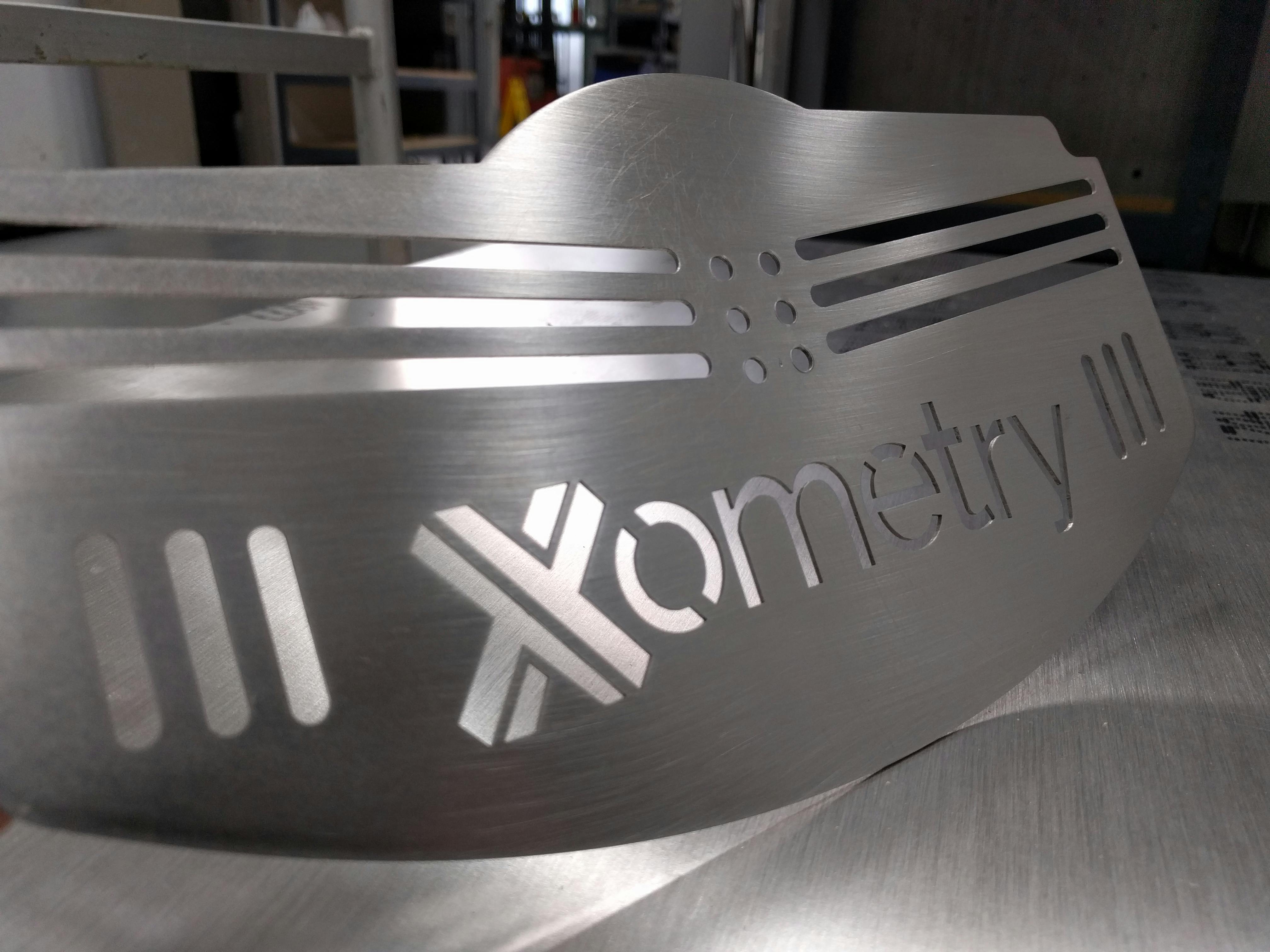
5. Maintain Uniform Bend Orientation
Bends in the same plane should be designed in the same direction to avoid part reorientation, which will save both money and time. Keeping a consistent bend radius will also make parts more cost-effective. For more information check out our blog post on the basics of bending sheet metal.
Xometry offers sheet metal fabrication in addition to CNC machining, 3D printing services, injection molding, and urethane casting. Get an instant quote on your parts using our newest Xometry Instant Quoting Engine℠.
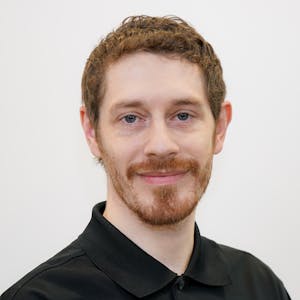