Polycarbonate is an amorphous engineering thermoplastic. It is one of the toughest thermoplastics that can also be made optically clear. Polycarbonate is often used as a lighter and stronger substitute for glass. It is tougher than acrylic (another popular transparent thermoplastic). Polycarbonate panels do have two significant disadvantages, however: they tend to become brittle and yellow when exposed to UV light, and they scratch easily. It must be noted that both of these undesirable properties can be counteracted with specialized coatings. The image below is an example of solid polycarbonate sheets:
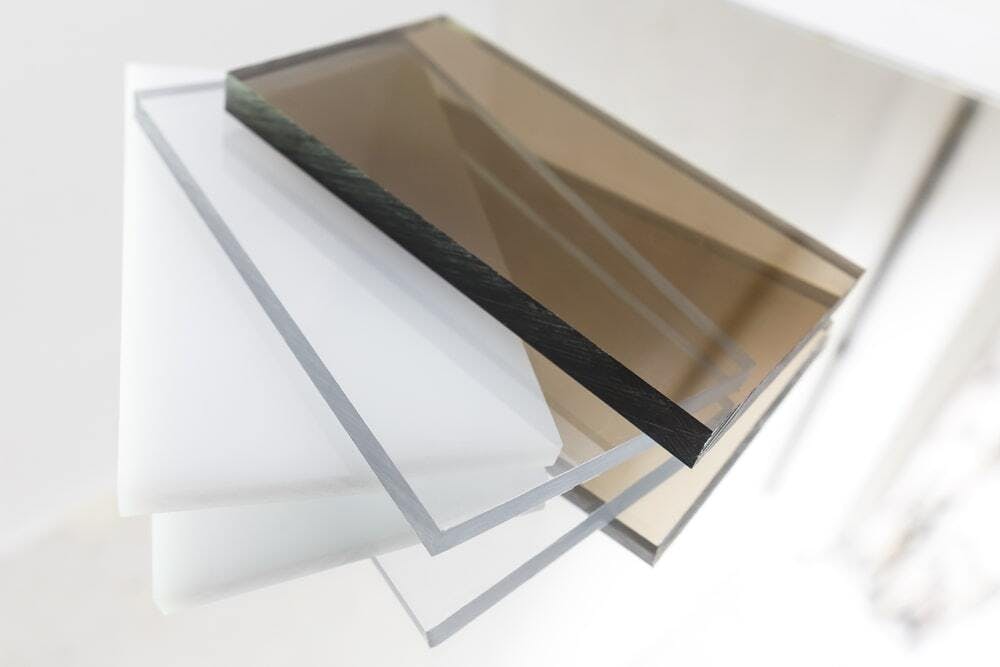
Brown, white, and transparent polycarbonate sheets.
Image Credit: Cat Us/Shutterstock.com
Its unique combination of properties means polycarbonate has a wide range of uses such as: bullet-resistant windows, machine guards, two-way mirrors, commercial windows, and barriers. This article will discuss the 6 common types of polycarbonate: clear, bullet-proof, anti-static, mirrored, abrasion-resistant, and colored or tinted polycarbonates. It will also describe the use cases and advantages of each.
1. Clear Polycarbonate
Polycarbonate transparent sheeting transmits light almost as well as glass. This makes it ideal for applications that require optical clarity. A clear polycarbonate sheet can withstand impacts that would easily shatter glass. It’s also stronger than acrylic, another common transparent thermoplastic. Due to these properties, polycarbonate is used on products that need to be optically clear but also impact-resistant. The applications can include: machine guards, car headlamp covers, and construction vehicle windshields.
2. Bulletproof Polycarbonate
Some types of polycarbonate can be considered bullet-resistant and offer varying degrees of protection depending on several factors. The level of protection depends on the type of polycarbonate used, the lamination method, and the overall polycarbonate sheet thickness. Bullet resistance is typically measured on the UL scale with level 1 offering the least protection and level 3 offering the most. Polycarbonate sheets of a ¾” thickness can achieve UL level 1. Bullet-resistant polycarbonates are good for applications that demand high levels of impact resistance but a low part mass. Aerolite polycarbonate sheet is one of the most common types of polycarbonate that is used for bullet-resistant applications.
3. Anti Static Polycarbonate
Certain types of polycarbonate have anti-static properties. Another term for anti-static is ESD (Electro Static Dissipative), meaning that static electricity cannot build up on the material’s surfaces. This makes anti-static polycarbonate ideal for components that come into contact with sensitive electronic equipment that might be damaged by static discharge. Anti-static polycarbonate has a special coating that prevents the build-up of static charges on its surface. Typical applications can include: assembly surfaces for electronic components and electronics enclosures.
4. Mirrored Polycarbonate
Mirrored polycarbonate contains a reflective film that can either behave as a normal mirror or as a two-way mirror. Because polycarbonate is so tough, it can be used to replace heavier and more delicate glass mirrors. Polycarbonate mirrors are often found in the bathrooms aboard commercial aircraft and camper vans.
Two-way polycarbonate mirrors are used in interrogation rooms. When the interrogation room is brightly lit, the reflective coating acts as an ordinary mirror to those inside. Some light passes through, however, so people in the darker observer room can see through.
5. Abrasion-Resistant Polycarbonate
Though standard polycarbonate sheeting scratches easily, there are types of polycarbonate that are abrasion-resistant. Abrasion-resistant Polycarbonate has a scratch-resistant coating on each side of the sheet to improve its resilience. One such coating is known as DLC (Diamond-like carbon) which is applied via a PACVD (Plasma-Assisted Chemical Vapor Deposition) process. PACVD is a low-temperature process that is ideal for materials like plastics with relatively low melting temperatures. Abrasion-resistant Polycarbonate is typically used in applications such as optical disks wherein scratches can reduce product performance.
6. Colored/Tinted Polycarbonate
Most types of polycarbonate are available in multiple different sheet colors. As is the case with many thermoplastics, polycarbonate can be colored or tinted. Coloration primarily serves aesthetic purposes. Some serve more functional purposes, though; specialized tints can be added to polycarbonate panels to reflect solar radiation, keeping rooms cooler.
Which Type of Polycarbonate is Used in Roofing?
The polycarbonate used in roofing must be UV-resistant to prevent it from yellowing and becoming brittle. Some multi-pane configurations are available to improve the panels’ insulative capabilities. Polycarbonate is a tough, impact-resistant material that can allow lots of natural light into a structure. The combination of durability and light transmission makes polycarbonate sheets useful in greenhouses and skylights. Colored or tinted polycarbonate can also make for good roofing if light transmission is not desired.
Is Polycarbonate Durable?
Its amorphous crystal structure makes polycarbonate one of the most durable thermoplastics. It has excellent strength, toughness, and temperature resistance. Polycarbonate tends to scratch easily but can be protected using special hard coatings such as DLC (Diamond-like Carbon).
Is Polycarbonate Opaque?
Polycarbonate is typically used in its transparent state but can be made to be opaque if desired. Color pigments can be added to polycarbonate to make it opaque. Standard transparent polycarbonate sheeting will yellow with prolonged exposure to UV radiation. Polycarbonate items that will be exposed to UV radiation are often made opaque to avoid this unsightly yellowing effect.
Which Type of Polycarbonate is Best for Making Gates?
Both colored and transparent polycarbonate panels are suitable for making gates. Transparent polycarbonate must be UV resistant, however. In many cases, metal gates are lined with polycarbonate sheets so the whole structure is more secure and resistant to damage. Thinner polycarbonate sheets may be extruded in a corrugated pattern to keep the surface stiff but save on material. Anyone looking to employ polycarbonate plastic sheets for gates should make use of UV-resistant polycarbonate sheets to prevent the panels from yellowing and becoming brittle over time due to exposure to sunlight.
Summary
This article provided a summary of 6 common types of polycarbonate and the properties of each. Xometry offers polycarbonate sheets in a range of different sizes.
Disclaimer
The content appearing on this webpage is for informational purposes only. Xometry makes no representation or warranty of any kind, be it expressed or implied, as to the accuracy, completeness, or validity of the information. Any performance parameters, geometric tolerances, specific design features, quality and types of materials, or processes should not be inferred to represent what will be delivered by third-party suppliers or manufacturers through Xometry’s network. Buyers seeking quotes for parts are responsible for defining the specific requirements for those parts. Please refer to our terms and conditions for more information.
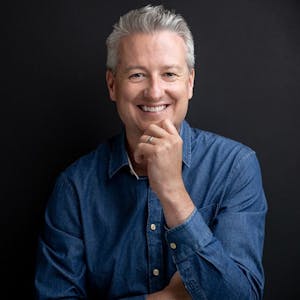